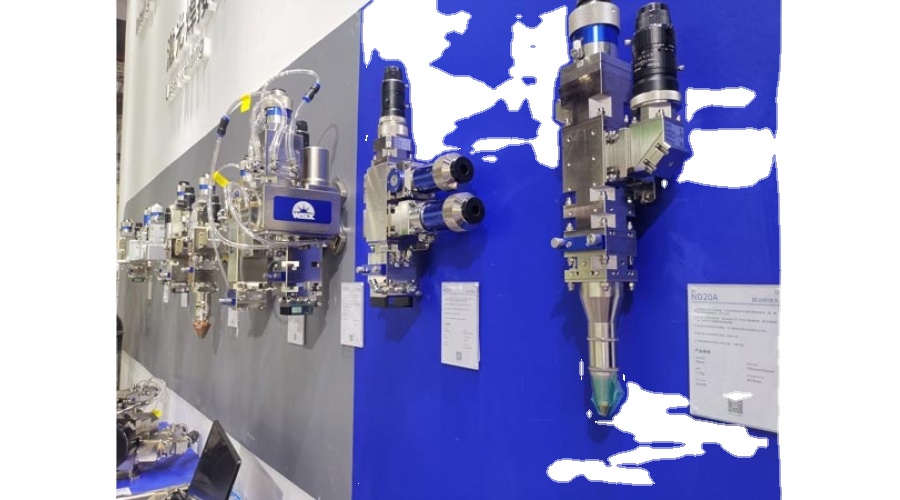
Lightweight laser welding tips are specialized tools used to join materials together during the laser welding process. This component is part of a laser welding system and plays a vital role in accurately delivering the laser beam to the welding area.
Compact design: The head should be designed to be lightweight and compact, allowing easy integration into different manufacturing setups. This is particularly important in applications where space is limited or where the welding head needs to be mounted on a robotic arm.
Portability: Portability is a key advantage of lightweight laser welding joints. It allows the flexibility to move welding equipment to different locations within a manufacturing facility and even between facilities.
High precision: The head must provide high precision in the direction of the laser beam to the welding point. This is critical for achieving precise and consistent welding, especially in applications that require fine detail or in industries such as electronics where precision is critical.
Cooling system: Laser welding generates heat, and a cooling system is necessary to prevent the welding head from overheating. Effective cooling mechanisms should be incorporated into the design to maintain equipment stability and longevity.
Adaptability: The head should be adaptable to different types of laser and welding processes. This flexibility allows it to be used in a variety of applications and different materials.
User-friendly interface: A user-friendly interface is essential for easy operation and setup. This can include features such as touch screens, intuitive controls and programming interfaces that simplify configuration of welding parameters.
Automation compatibility: For automated manufacturing processes, lightweight laser welding joints should be compatible with robotic systems. This ensures seamless integration with automated production lines, increasing efficiency and reducing labor requirements.
Dust and Debris Protection: In industrial environments, there may be dust or debris that affects the performance of laser welding joints. The design should include protective measures to minimize the effects of external contaminants.
Easy maintenance: Easy maintenance and cleaning are important factors in keeping laser welding joints in optimal working condition. This helps minimize downtime and ensure consistent performance.
Safety features: Incorporating safety features, such as laser beam shielding and interlocking systems, are essential to protect operators and ensure compliance with safety standards.
When selecting a lightweight laser welding joint, the specific requirements of the application and welding material must be considered. Additionally, for seamless integration into the manufacturing process, compatibility with existing equipment and overall workflow should be considered.