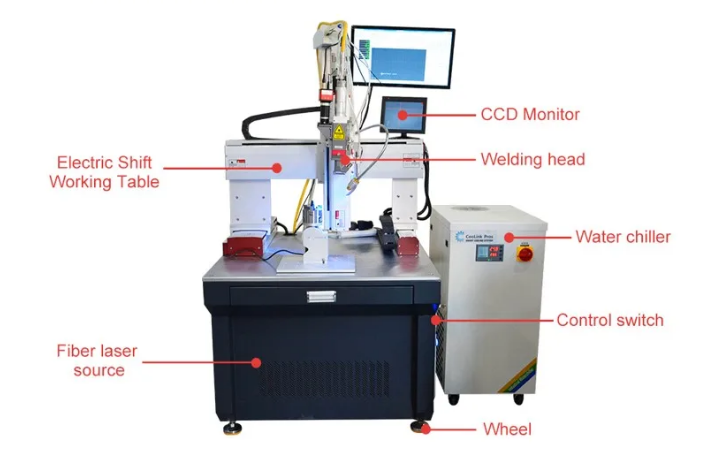
Aluminum laser welding machines are specifically designed to address the unique properties of aluminum as a material. Aluminum has high thermal conductivity and reflectivity, which makes welding challenging using traditional methods. Laser welding provides a precise and efficient solution for joining aluminum components.
A key factor in aluminum laser welding machines is the choice of laser type. Fiber lasers are often the first choice for aluminum welding due to their excellent beam quality and absorption characteristics. The wavelength of the fiber laser is well suited for efficient energy absorption in aluminum, promoting efficient melting and bonding.
The power of the laser source is another important consideration. For thicker aluminum profiles or applications requiring deep penetration, higher power lasers are typically required. Pulse shaping and control capabilities are also important, allowing operators to tailor the welding process to the specific requirements of aluminum welding.
Additionally, these machines often feature advanced cooling systems to manage the heat generated during the welding process, ensuring consistent and reliable performance. Precision control mechanisms, such as CNC integration, help achieve precise welding with minimal distortion.
In summary, aluminum laser welding machines are characterized by their choice of laser type, power, and advanced control features that address the challenges posed by the unique properties of aluminum and provide precise and efficient solutions for aluminum welding applications.