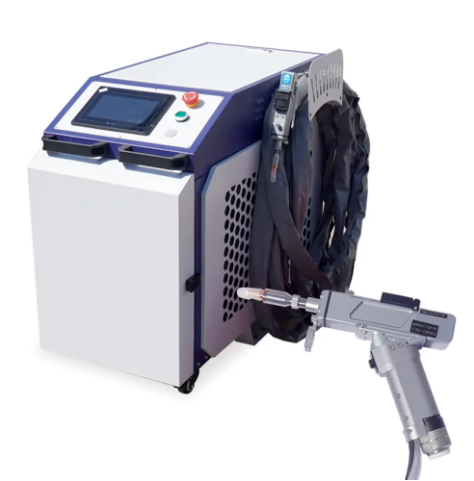
A versatile laser welding device designed to provide flexibility and precision using laser technology in a variety of welding applications. Laser welding is a process that uses a laser beam to join materials through melting and solidification.
Multi-wavelength capability:
Versatile laser welding equipment can support multiple wavelengths, allowing you to work with different materials. For example, fiber lasers are typically used for metal welding, while other wavelengths may be suitable for plastics or other materials.
Pulse width and frequency control:
The ability to control the pulse width and frequency of a laser beam is critical to regulating heat input during welding. This feature provides the flexibility to handle a variety of materials and thicknesses.
Power adaptability:
Look for laser welding equipment with adjustable power settings. Different materials and welding requirements may require different levels of laser power for optimal results.
Precision and accuracy:
A versatile laser welder should provide high precision and accuracy, especially when working with fine or intricate details. This is critical for applications in industries such as electronics, medical devices and jewelry.
Automatic Control System:
Some advanced laser welding equipment comes with automatic control systems that can be programmed for specific welding modes or tasks. This feature increases efficiency and repeatability, especially in production environments.
Optical fiber transmission system:
Laser welding equipment with fiber optic delivery systems provides the flexibility to reach different parts of the workpiece. Fiber optic transmission systems are also more durable and can more easily operate in various welding positions.
Real-time monitoring and feedback:
Real-time monitoring systems, such as cameras or sensors, can provide feedback on the welding process. This helps the operator make adjustments as needed and ensures weld quality.
cooling system:
A reliable cooling system is crucial to maintaining the normal operating temperature of laser welding equipment, especially when used for extended periods of time. Overheating can affect the performance and life of your equipment.
Friendly user interface:
An intuitive and user-friendly interface for easy control and programming of laser welding parameters. A touchscreen display and easy-to-navigate menus enhance the user experience.
Security features:
Laser safety features, such as containment systems and interlocking mechanisms, are critical to ensuring operator safety. Complying with laser safety standards is critical.
Material Compatibility:
Make sure your laser welding equipment is compatible with a variety of materials, including metals, plastics and other composites. This expands the range of applications of the device.
Portability and workspace integration:
Depending on your needs, consider the portability of your laser welding equipment and its compatibility with your workspace. Some equipment is designed for integration into production lines, while other equipment may be better suited for mobile or field applications.
When selecting versatile laser welding equipment, consider the specific materials and applications you will be working with, as well as the level of automation and precision required for your project. Always follow safety guidelines and ensure that operators using laser welding equipment are properly trained.