In laser cutting, achieving high-precision synchronization of servo drives is key to ensuring cutting accuracy and quality. Here are some strategies and best practices to achieve this goal:
Closed-loop feedback system:
Use encoders and resolvers to provide real-time feedback on the position and speed of servo motors. This helps to make immediate adjustments to keep the motors synchronized.
High-resolution encoders:
Use high-resolution encoders to provide precise position feedback and improve the accuracy of servo control.
Advanced motion controllers:
Implement motion controllers capable of high-speed and high-precision calculations. These controllers should support multi-axis synchronization and interpolation.
Real-time communication protocols:
Use real-time communication protocols such as EtherCAT, PROFINET IRT, or SERCOS III. These protocols ensure that data is transmitted with minimal latency and jitter.
CNC system:
Use a CNC control system designed specifically for laser cutting applications. The system is optimized for high-precision coordination of multiple servo axes.
Servo parameter tuning:
Fine-tune servo parameters (such as PID gains) to optimize the response of each servo motor. Proper tuning helps reduce overshoot, oscillation, and lag.
Temperature Compensation:
Implement temperature compensation techniques to account for thermal expansion and contraction, which can affect the accuracy of the servo motor.
Mechanical Design:
Ensure that the mechanical design of the system minimizes backlash, flex, and other sources of mechanical error. This includes using high-precision gears, couplings, and bearings.
Calibration and Maintenance:
Perform regular calibration and maintenance on the system to ensure that all components are functioning properly within specified tolerances.
Software Algorithms:
Utilize advanced software algorithms for path planning and motion control. Techniques like forward-looking processing and jerk control can improve the accuracy of motion.
Synchronization Mechanisms:
Implement synchronization mechanisms such as a master-slave configuration, where one servo drive acts as the master and the other drives follow its lead.
Vibration Attenuation:
Use vibration damping techniques to reduce the effects of mechanical vibration on the accuracy of the servo motor.
Power Quality:
Ensure that the power supply to the servo drive is stable and clean to avoid fluctuations that can affect its performance.
By combining these techniques, you can achieve high-precision synchronization of servo drives in laser cutting applications, thereby improving the accuracy and quality of the final product.
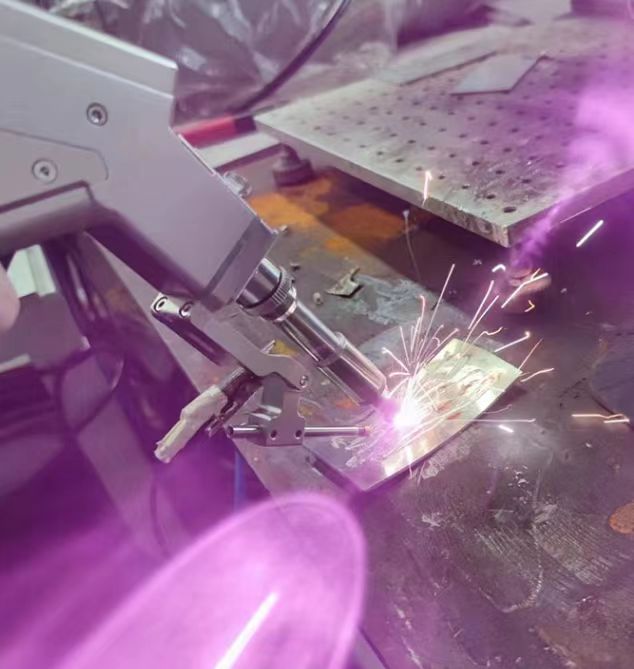